Recently, the "Government Work Report" was officially released in 2023. The government work report also made important arrangements for the development of industrial industry, emphasizing "accelerating the construction of a modern industrial system, accelerating the digital transformation of traditional industries and small and medium-sized enterprises, and striving to improve the level of high-end, intelligent and green." In view of the difficulties encountered in the process of digital transformation of manufacturing enterprises, Zhang Jianwei, director of Lenovo Consulting and Delivery Center, shared the successful cases of digital intelligence transformation of Lenovo-empowered intelligent manufacturing enterprises, which can provide Lenovo’s practical experience for manufacturing transformation.
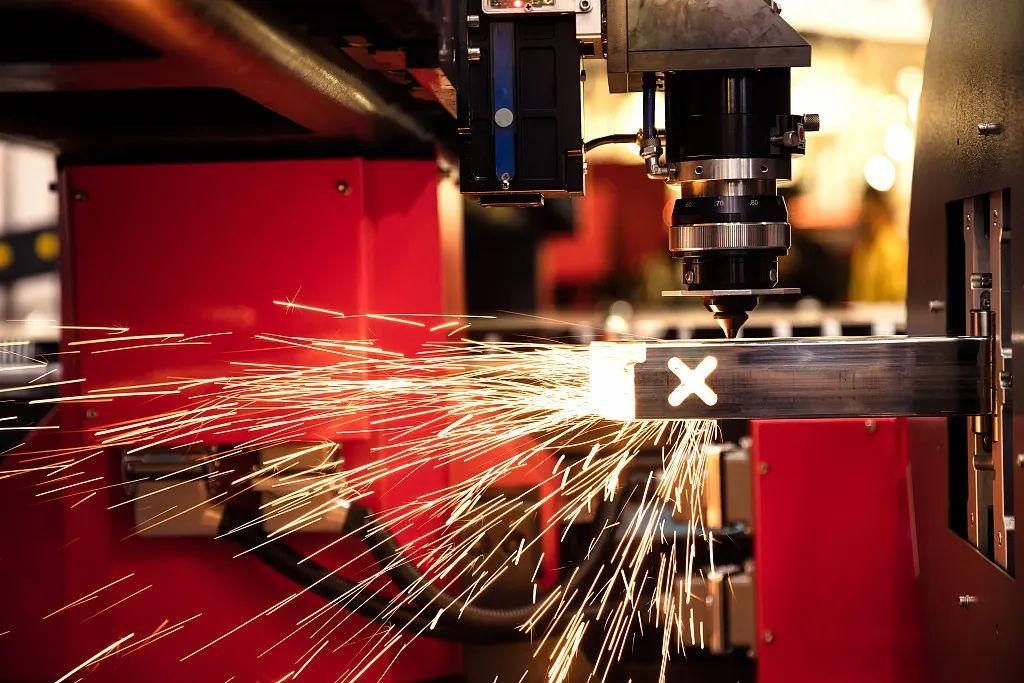
The concept of intelligent manufacturing is not a new topic in China. Looking at the development market of enterprises in China, we summarize the core problems that hinder the development of intelligent manufacturing as follows:
Lack of practical methods:With practical methods, enterprises can put their ideas to the ground. At this stage, enterprises are more discussing concepts and strategies, and lack the implementation methods of strategy landing;
Lack of valuable entry point:China’s manufacturing industry is in urgent need of intelligent manufacturing, and the value that intelligent manufacturing can bring to China’s manufacturing industry is also considerable, but from which level and angle should we cut in? It is an important problem that puzzles the CIO/CTO of enterprises;
Lack of best practices:In the absence of best practice cases, China enterprises should rely more on their own self-reliance, cross the river by feeling the stones, and open up a road of their own practice.
As a representative enterprise of China’s advanced manufacturing industry, Lenovo believes that the core of intelligent manufacturing of China enterprises is to aggregate total data, intelligently drive business changes, realize the continuous realization of digital value by solving practical business problems, and then complete the intelligent iterative upgrading of manufacturing industry. To this end, Lenovo has built an intelligent manufacturing panorama with data-driven intelligence as the core. Simply put, Lenovo Intelligent Manufacturing Panorama can be divided into three layers:
The first layer: the element layer.
Focus on the manufacturing factors concerned by the traditional manufacturing industry, including labor equipment, raw materials, process environment and a series of contents, and realize the complete digitalization of the basic level through the digitalization and intelligent upgrading of the manufacturing factors; Realize the interconnection of all things through advanced digital technologies such as industrial internet, integrate production factors together, better form a whole, and play the relevant value of production factors from the perspective of the whole value chain;
The second layer: the operation layer
Based on the interconnection of everything in the factor layer, the data generated in the actual production and operation process of enterprises, such as scheduling, manufacturing, supply chain coordination, logistics management and other key links, are integrated into the business layer, and the business development iteration is driven by data value, thus realizing the realization of data value and intelligent manufacturing value;
The third layer: intelligence
Form a relatively primitive intelligent plan, and carry out a series of business intelligence such as intelligent manufacturing and intelligent supply chain collaboration. After realizing business intelligence, based on the complete digitization of output data and elements, it can realize global visibility and intelligent decision-making for managers, and then move towards the final so-called data-driven. Without decision-making by human beings and intervention by managers, the data-driven business is realized completely through data, artificial intelligence and related digital technologies, and the continuous optimization of the operation and management of the whole enterprise is realized.
After constructing the panorama of intelligent manufacturing transformation, Lenovo carried out the practice of internalization and externalization in the following years, which brought many values to the actual development of manufacturing industry:
01
Intelligent manufacturing scene landing
Optimization of battery manufacturing process
New energy battery is one of the hot development industries in the world. Based on advanced technologies such as big data and machine learning, Lenovo applied LEAP HD and LEAP AI platforms to build a capacity prediction model to optimize the constant volume process of energy storage batteries.
In the process of battery production, the battery capacity needs to be fixed and divided to determine whether the battery meets the standards. In this process, enterprises are faced with problems such as long time consumption, high space occupation, high cost and high labor consumption. In the whole process optimization scheme, Lenovo has effectively helped customers to improve the on-time delivery rate, inventory cost, capacity utilization rate and comprehensive energy efficiency from three perspectives: key process data processing, accurate model prediction and sustainable development, and realized the optimization of battery constant volume and capacity separation process:
Business consultation:Clear up the key process sections through consultation and communication, including what are the key parameters that affect the quality? Where are the relevant data that affect these parameters? What are the data sources? Help customers to understand the current situation, plan their goals and prepare relevant plans;
Data integration:Through big data technology, a series of data such as related processes and equipment quality inspection are integrated to lay a good foundation for the later artificial intelligence algorithm and ensure the smooth operation of computing power;
AI algorithm implementation:Through the preliminary analysis, the specific data content and the specific core parameters affecting the process are clarified, and the relevant business analysis is carried out to help customers jointly optimize the relevant parameters, so as to achieve the final process goal optimization.
In the process of upgrading and optimization, Lenovo builds a dimension reduction model through logical modeling, including related methods of artificial intelligence and collective learning, to ensure the stability of large-scale data processing, the accuracy of prediction model and the guarantee of sustainable development, and solves the bottleneck of prediction model in actual production and operation by applying multi-strategy network optimization and machine learning model.
After the project was put into production, the construction period in the whole production process was shortened from six days to one day; Product inspection is realized by artificial intelligence algorithm, which improves the overall inspection efficiency and site utilization rate by 30%; Also with the help of artificial intelligence, the number of technicians decreased from 20 to 10. It is predicted that the optimization scheme can save about 270 million manufacturing costs for the production of single battery every year.
02
Intelligent manufacturing scene landing
Improvement of warehousing logistics performance
In the field of logistics, the focus of transformation is more on the optimization and management of warehousing. Many enterprises, especially those like Lenovo, take up a large part of the inventory cost. If there are too many offline warehouses, it will affect the inventory cost and occupy the whole production market, which may lead to risks for the site and space. If there are too few side libraries, it will lead to insufficient capacity utilization and unable to carry out continuous production reasonably. These two problems can be overcome by enterprises through the warehousing and logistics solutions of digital factories.
Line-side warehouse is also the storage part, which involves not only the warehouse, but also related processes and related equipment, including related information systems. To solve these problems, a complete solution is needed.
In the past, the solutions in the market were mostly piecemeal. If the equipment efficiency is not high, change the equipment and change it to more intelligent equipment. If the information communication is not smooth, increase the information system; If the process is not clear, sort out the process. In fact, this has brought great waste to the investment of enterprises, and the cycle and yield of the whole project will also be greatly reduced. On this issue, Lenovo has adopted a three-part approach.
First of all, help customers smooth the process through preliminary consultation, and identify the pain points, difficulties and problems to be solved in the online library management process. Then, based on the overall scheme, aiming at the combination of hardware and software and the combination of reality and reality, the related storage equipment is upgraded.
At the same time, digital systems such as WMS and WCS can fully mobilize the factors of production between equipment and people, so that these factors of production can better form a closed loop of value under the drive of informationization and digitalization, and improve the overall efficiency, thereby improving the management and application efficiency of the entire line-side library, reducing inventory and improving the continuous productivity of the production line. After practical application, the scheme has improved the overall storage capacity by more than 15%, the distribution efficiency of the roadside warehouse by 25%, and the accuracy of inventory delivery by 100%.
03
Intelligent manufacturing scene landing
Optimization of planned production scheduling system
As a upstart in the industry, this customer has developed very rapidly in the high-tech industry in recent years, and its business is growing at a rate of 200% or even 300% every year, which also brings great problems. The high-speed business development makes it difficult for its existing information support auxiliary means to provide the required support, which in turn leads to the lower and lower operating efficiency of enterprises, and it is difficult for managers at all levels to control the overall situation and provide scientific and accurate relevant guidance to the business.
Based on this, Lenovo packaged its own digital supply chain package, and used intelligent planning and production scheduling technology as the best practice of endogenous and exogenous strategy landing. Through Lenovo’s similar global delivery mode and complex supply chain network system, it empowered customers to realize the overall digital ability improvement. After the implementation of the project, it has effectively helped customers to improve the on-time delivery rate, inventory cost and capacity utilization rate, including the comprehensive number of people and energy efficiency.
In addition, Lenovo has joined hands with manufacturing enterprises in chemical fiber manufacturing, automobile manufacturing, wind power manufacturing, hydropower manufacturing, hardware manufacturing and other fields to provide digital and intelligent transformation services from hardware to software, which has achieved a comprehensive improvement in the hard power of enterprises.
In the future, Lenovo hopes to co-create its own business practice with its customers’ business, integrate its own computing power and infrastructure capabilities with its customers’ business development scenarios, and join hands with more manufacturing partners to go further and faster in the process of digital modernization and transformation.